General O&M
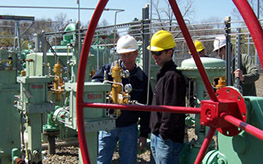
Precision Pipeline Solutions, LLC (PPS) partners with utilities, power plants, and other end users to fulfill all pipeline operations and regulatory compliance maintenance requirements to manage natural gas systems. We perform all services which a utility has historically completed internally to operate its system with service offerings ranging from hands-on fieldwork to DIMP program consulting.
Active Service Offering
|
|
PPS Personnel
Our personnel are diversely experienced from troubleshooting many different clients’ pipeline systems; this is what allows us to adapt our training to work on your footprint. All our technicians are Operator Qualified and are experienced problem solvers.
PPS Methodology
We assign a specific Client Relationship Manager (CRM) to your organization that will be the main point of contact and a problem solving partner. Our CRM will help connect your needs with the appropriate staff and operating groups internal to PPS.
Our Operation Managers are Subject Matter Experts in their own fields and our company is aligned to benefit from these strengths by functioning in these operations clusters: Construction Services, Gas Technical Services, Surveys & Inspections, Meter Exchange, Electric Services, and Professional Services.
PPS Safety & Quality
PPS maintains a company-wide safety program, with many specific safety initiatives focused on the high risk areas of the work day. Field Managers complete Tailboard Talks discussing ways to be alert and mitigate typical and environment-specific hazards, and each technician is issued a standard kit including PPE, fire extinguisher, and traffic/vehicle protection.
PPS maintains a multi-layer approach to Quality: 1) Personal Accountability of each technician, 2) Project-level Quality Control performed by supervisory personnel, and 3) Company-wide Quality Assurance.
Coating Services
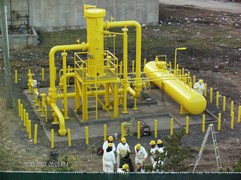
Precision Pipeline Solutions, LLC (PPS) specializes with coating systems in-situ (in-field) to apply the most appropriate coating to extend the useful life of existing assets. Our services extend through assessment and selection, coating removal and abatement, to coating application. We service clients in all environments including but not limited to subsurface manholes, regulator stations, and protected wetland preserve.
Active Service Offering
|
|
Personnel - Regulator Operator Qualified Oversight
Our operator qualified personnel are well experienced in coating systems and are also trained in other natural gas related subjects to increase their knowledge base about the mechanisms they are working on including pressure control and leak survey.
A fully qualified pressure control technician is assigned to design the workflow to ensure that sensitive instruments in regulator stations are appropriately protected and maintained throughout the process. Our staff of pressure control technicians can also blow-down, gas-in or switch-over regulation runs to allow for the coating process to be completed.
Equipment & Site Profile
We have developed several mobilization systems which allow our coating teams to be portable, low profile and efficient.
We have experience working in many different types of site conditions, each requiring a unique setup to get the job done in a discreet and effective manner, including: metropolitan, industrial, residential, subsurface, tunnel, wetland or protected, and transmission right-of-way.
Environmental
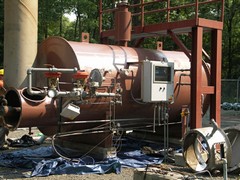
KONICA MINOLTA DIGITAL CAMERA
Our projects include constraints which require high level containment wherein either the coating is considered hazardous (such as lead-based paint) or the environment is fragile and requires a very high degree of protection to sustain the ecosystem. We create a site-specific containment plan and as necessary employ the use of high-capacity air circulators, dust collectors, and other containment devices to ensure all coating by-products are mitigated from the site.
Our Approach & Coating Types
We approach each coating project with the goal of best serving our customer’s needs, not selling a particular service.
This is why we have experience with a very diverse array of coating products. After reviewing the standards in place at each utility and utilizing our experience and considering the particular site conditions, we recommend an approach with options to best resolve the problem within the client’s budget.
We have found many innovative ways to be the solution to our clients’ coating problems.
One of our innovations has been to successfully develop methods to bring Thermal Spray Aluminum (TSA) coating systems to existing in-field pipelines.
For over a century, TSA has provided the longest lasting, most cost effective way to protect steel from atmospheric and water immersion in the petrochemical, off shore, and military applications.
Thermal Spray Aluminum is an anodic coating process which mitigates corrosion in three ways:
- Creating a barrier to the environment
- Acting as a sacrificial anode for any holidays
- Electrically passivate the surface of the steel
The application cost of TSA coating is similar to a three coat immersion grade paint coating, but can be maintenance free for over 20 years!
Thermal Spray Services
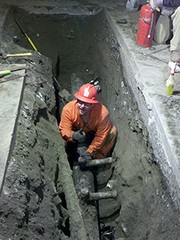
Lower your operating costs and reduce your maintenance budget by…
Introducing a coating system that can OUTLIVE your current process by multiple lifetimes
- Are you concerned that corroding equipment might develop into a safety issue?
- Do you have corrosion issues in vaults or manholes – regulators, valves, transformers, supports, or other equipment?
- Are you confident that your current painting/coating program is protecting those hard to reach points on your equipment (such as spaces between flanges, or behind nuts)?
- Is atmospheric corrosion inspection and mitigation an ongoing expense in your maintenance budget?
Stop coating and painting your corroding equipment year after year!
Consider a properly specified and professionally applied protective thermal spray anodic coating system.
In most applications, you can consider it a lifetime coating system.
For over a century, thermal spray anodic coatings have provided the longest lasting, most cost effective way to protect steel from atmospheric and water immersion corrosion in civil, petrochemical, military, and off shore applications. Mean time between corrosion inspections has been increased from 3 years to 20 years in many of these applications.
In the thermal spray coating process, an anodic metal (usually aluminum or zinc) is thermally sprayed onto the equipment that is to be coated. The thermally applied coating mitigates corrosion in three ways –
1) by creating a barrier to the environment (eliminating the electrolyte from the corrosion cell),
2) by acting as a sacrificial anode for any nicks or holidays that occur on the coating over time, and
3) by electrically passivating the surface of steel, so that corrosion cells no longer exist.
The process takes the place of paints and epoxies, and has superior longevity to these traditional coating methods. We incorporate the most up-to-date requirements from industry organizations such as NACE, SSPC, AWS, and EFC in all our coating solutions.
Previously, thermal spray anodic coating systems could only be applied during prefabrication, but the thermal spray experts at Precision Pipeline Solutions have developed the tools and procedures to allow for the in-field application of this coating technology at a cost similar to three coat immersion grade paint coatings.
PPS Coating Services also provides lead abatement, coating removal, and traditional coating services.